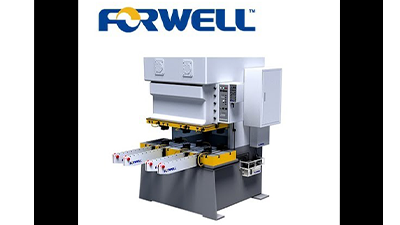
Quick Die Change System | FORWELL
Forwell’s Quick Die Change System is an automatic die changing system that can be specifically designed for hydraulic and mechanical power presses and press production lines. This system automates the die changing process and provides increased speed, efficiency and productivity to a workshop. The Quick Die Change System not only reduces die change time, but also promotes diverse small batch production runs and streamlines production management.
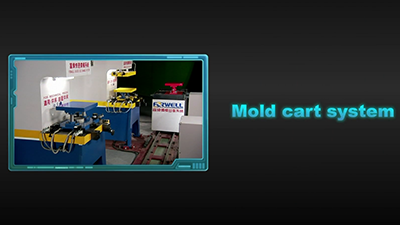
Mold Cart | FORWELL
Mold Cart - Mold Cart System-Forwell Features -Fully automated die or mold changing - High precision die or mold placement - Increased safety and efficiency - Can serve multiple production lines at once - Multiple layout configurations System Introduction : Forwell's Die / Mold Cart System provides automatic die or mold changes for a range of different machines, such as plastic injection molding machines, plastic extrusion machines and press machines. This Die / Mold Cart system offers very fast, efficient and safe die and mold changes, using an advanced cart on rails system. Conventional die or mold changes can often take over an hour, but with the Die / Mold Cart System, die or mold changes are automatically completed in just a fraction of the time. Using this system, all procedures from die transfer and changing, to positioning and clamping is carried out by this system, resulting in extremely accurate die or mold changes. As the Die / Mold Cart System offers very precise die or mold changes, many operational issues can be avoided such as locking screws breaking when hand tightened, and incorrect mold alignment resulting in damage to the mold or production equipment. The Die / Mold Cart System also massively increases safety and efficiency, by allowing for automatic operations and making it feasible to perform many small batch production runs. Another great feature of this system is that it can be configured to specific user needs, different production facilities and serve multiple production lines at once.
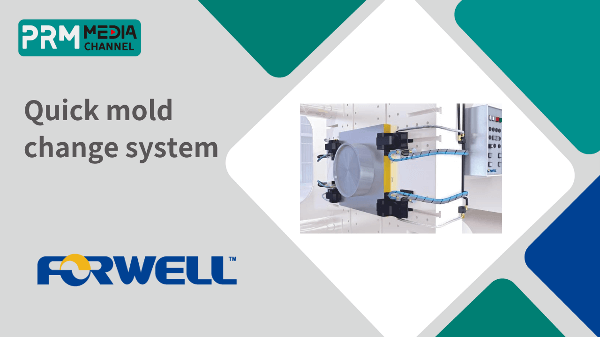
Quick mold change system|QMCS|for Injection molding|Sistemas de cambio rápido del molde|FORWELL
Forwell has been a pioneer of Quick Mold Change Systems for many years. With over 20 years of experience in developing these systems they can offer you the best for your molding operations. These fully customizable Quick Mold Change Systems drastically minimize setup times, maximize efficiency and increase safety. Forwell’s Quick Mold Change System can be designed to fit almost any injection molding machine and mold casting machine to allow for quicker mold change times, resulting in shorter machine down time and increased productivity. This system uses a special mold clamp that does not require a cut out on the mold, increasing its application versatility and allowing it to be used with a large number of different molds. Quick Mold Change Systems can rapidly transform your workshop, allowing for easy changeover for small batches, reduced labor costs and reduced stock holding. Coupling this system with a Mold Cart System will allow for fully automatic mold changing, further increasing the efficiency and productivity of your manufacturing operations. When installing a Quick Mold Change System for your injection molding and mold casting operations there are a number of direct and indirect benefits. Review the following table to see an overview of all of these benefits. Indirect Benefits Die Standardization Press Standardization Increased Safety Improved Working Environment Increased Competitiveness Direct Benefits Reduction in Die Change Time Efficient Small Batch Runs Reduced Stock Handling Higher Productivity and Quality Reduction in Labor Costs
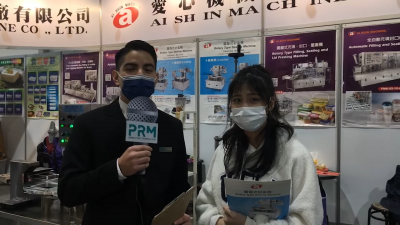
Food Packaging Solutions | AI SHIN Interview
At the recent TAIPEI PACK exhibition, PRM Media Channel had an interview with AI SHIN MACHINE CO., LTD. to discuss about the current situations in the packaging industry, upgrade in the service of the company due to current pandemic, also the machinery showcased. AI SHIN is famous for its Automatic Filling & Sealing Packing Machines. The company specialized in manufacturing high speed packing machines for food, filling and sealing liquid cups such as yogurt, juice and water cups. Let us know your opinion and the inquiry in the comment section. Stay tuned for the forthcoming interview videos and remember to subscribe to our social media channels for the similar videos!~ MAIN PRODUCTS/SERVICES OF AI SHIN: Automatic Filling Machine, Automatic Sealing Machine, Rotary Type Filling Machine, Filling & Sealing Machine, Bag Sealing Machines, Sealing & Packing Machines, Semi-automatic Sealer, Rotary Type Sealing Machine, Fully Automatic Box Filing & Sealing Machine for Butter, Capping Machine for Butter, Yogurt Packaging Machine, Pudding Filling & Sealing Machine, Frozen Food Filling & Sealing Machine, Cup/Bowl Instant Noodle Packing Machine, Packing Machinery, Cap Sealing Machine, Jam Cap Sealing Machine, Butter Filling/Sealing Machine, Cup Filling Sealing Machine ***
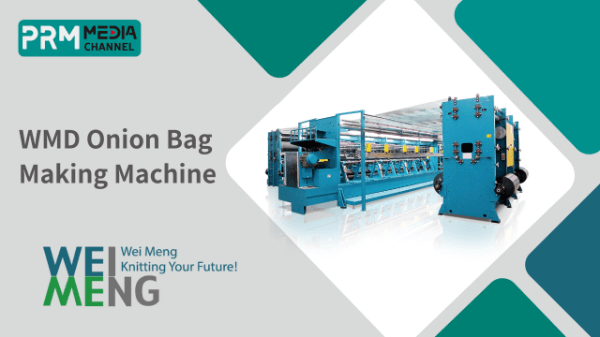
WEI MENG | WMD Onion Bag Making Machine
Our Double Needle Bar Raschel Machine is the perfect solution for businesses that need to produce high-quality, high-speed packing sacks. With a working width of 170 inches and gauges of 2 - 6 needles per inch, this machine can produce a variety of nets for different purposes. It is also ideal for producing onion bag machines, special wide nets, and double-layered nets. This machine is equipped with a high-speed warp supply system that ensures that your nets are produced quickly and efficiently. It also has a number of features that make it easy to use, including a user-friendly control panel and an automatic yarn tensioning system. If you are looking for a high-quality, high-speed Double Needle Bar Raschel Machine, then our machine is the perfect choice for you. Contact us today to learn more about our machines and how they can help your business. Double Needle Bar Raschel Machine is specially designed for onion bag and double layer nets making. This machine is applicable Yarn is HDPE flat yarn and monofilaments. Standard gauges machine 2 - 6 needle per inch, Maximum performance of the machine can up to 600rpm.
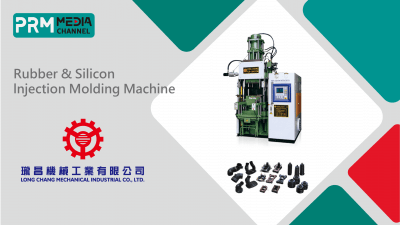
Rubber & Silicon lnjection Molding Machines | LONG CHANG
Long Chang is manufacturing the series of Rubber & Silicon injection Molding Machines, and Heated Compression Molding Machines etc. 【Machine Series】 Silicone Injection Molding Machine Rubber Injection Molding Machine Horizontal Automatic Rubber & Silicone Injection Molding Machine Single Body / Twin Body Vacuum Oil Hydraulic Compression Molding Machine Vacuum Rubber Oil Seal Hydraulic Compression Molding Machine Single Body / Twin Body Die-Moving & Ejection Compression Molding Machine Four Columns Type Oil Hydraulic Press EVA Foam Tire / Single Body Double Color Of Automatic Oil Hydraulic Compression Molding Machine 【Company Introduction】 Long Chang Mechanical lndustrial Co., Ltd. was established in 1971, under the leadership of president Huang Chin-Huo with the idea of "always be loyal to the obligation, give more than enough thought to operate the business" and demands "making the perfection more perfect" to be the target.
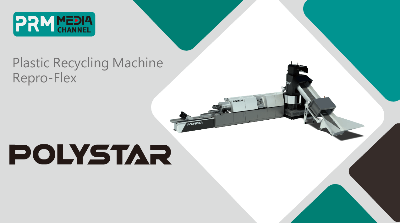
Plastic Recycling Machine, Repro-Flex | POLYSTAR
【Machine Features】 The one-step plastic pelletizing machine, Repro-Flex, combine cutting, extrusion, and pelletizing into one compact and efficient pelletizer line. The cutter-compactor of the plastic pelletizing machine prepares the plastic waste (PE plastic film and PP plastic film waste) into an ideal condition for the extrusion process and feeds the plastic waste directly into the extruder. This integrated system does not require a separate crusher, and therefore, eliminates the problem of inconsistent feeding, reduces space and labor costs, and has lower energy consumption. Simple in Design. Flexible in Operation. POLYSTAR is able to customize its machines regarding customers’ needs. How this pelletizing system works: 1. Feeding a. By belt conveyor Feeding of scraps is easy and automatically controlled depending on the amount of material input. b. By Nip roller Film-on-rolls can be fed at the same time. 2. Cutting and compacting The cutter compactor integrated cuts, dries, and compacts the material which enables a fast and stable feeding from the compactor directly into the extruder. 3. Degassing system The two-zone degassing can process plastic film with larger printed areas. 4. Filtration Screen change with a dual channel system for non-stop operation that also prevents plastic material from leaking. 5. Pelletization Water-ring pelletizing system, also known as hot die face pelletizing, the plastic comes from the recycling extruder and is directly cut by the rotating knives attached to the surface of the die head. 6. Final Product Round-shaped recycled pellets are produced and cooled inside the water ring immediately. 【Company Intro】 Headquartered in Taiwan, POLYSTAR has focused on the user-friendliness of its machines through continuous re-engineering, making recycling extremely “Simple” for its users – Easy operation and maintenance is what makes POLYSTAR the No.1 selling recycling machine today. Over the past 32 years, more than thousands of POLYSTAR recycling machines have helped worldwide plastic producers to reprocess their post-industrial (in-house) waste back into high-quality pellets in a simple and easy way.
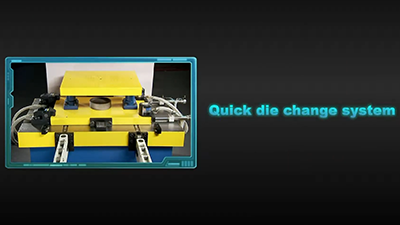
Quick Die Change | FORWELL
Quick Die Change - Quick Die Change System-qdcs-en-Forwell Features : • Decreased die change time • Designed for hydraulic and pneumatic presses • Increased efficiency • Reduced labor costs • Safer operations System Introduction : Forwell’s Quick Die Change System is an automatic die changing system that can be specifically designed for hydraulic and mechanical power presses and press production lines. This system automates the die changing process and provides increased speed, efficiency and productivity to a workshop. The Quick Die Change System not only reduces die change time, but also promotes diverse small batch production runs and streamlines production management. Quick Die Change Systems are becoming a standard for large manufacturers as they not only increase production efficiency, but also improve the overall working environment. The Automatic Die Change System can be built specifically for your machining requirements and will drastically reduce machine idle time during die changes, boosting your competitiveness. There are also a number of indirect benefits of installing a Quick Die Change System for your hydraulic and mechanical type press machines. Firstly, automated operations reduce labor expenses, but also reduce workshop accidents and the physical stresses on operators, making them more productive. Secondly, all dies can be changed without any modification allowing for the use of standardized die and press equipment, saving costs. Lastly, multiple presses can share a single Quick Die Change System, further economizing on costs and resulting in higher efficiency and productivity.
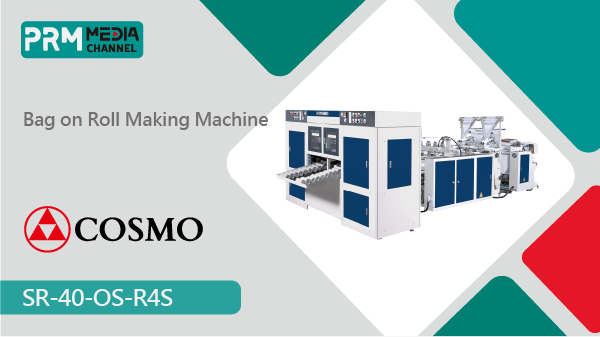
Bag on Roll Making Machine | COSMO
COSMO has many years of experience in bag making machines. We are still willing to have much more improvement and all the consumers are satisfied with the quality of machines offered to you. 【Machine Features】 2 lines coreless star sealed bag on roll making machine Oscillation film feeding & sealing system for stability and high out put Automatically reel changing system High production efficiency to save manpower and time Servo motor, as standard attachment, makes it easy to adjust the bag length and the production speed Computer control over the entire process From film roll to final bag, non-stop, one process flow Automatically stop when running out of film/ film feeding blocks or bags jam/ color scanning misses 【Company Introduction】 COSMO Machinery Co., Ltd. established in March 2001, is well-known for Taiwan manufacturing plastic bag making machinery with servo driving systems. The product from COSMO has the servo motor as standard attachment, makes it easy to adjust the bag length and the production speed, computer control over the entire process, component self-testing function available, high production efficiency to save manpower and time. Up to now, COSMO products are extensively exported to 100 countries spreading all over the world.
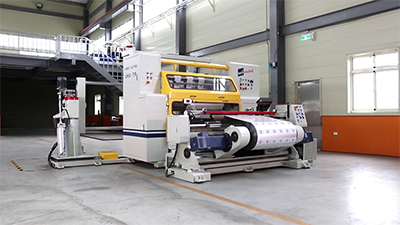
UHS Turret Slitter Rewinder - UHS-TR | WEBCONTROL
UHS Turret slitter rewinder The UHS-TR model is a proven fully automatic slitter rewinder, offered with many options to fulfill even the most demanding applications: - Cutting-edge slitting systems - Reliable auto cut and transfer - Advanced tension control - Combined with progressive differential winding technology - Precision and capacity at an affordable cost. - UHS-TR a must addition to any plant requiring quality Automatic knife positioning down to 25 mm slit width, double turret unwind, automated finished roll unloading systems are some of the available options to increase productivity, quality and decreasing operator influenced down time. Materials to be processed: Plastic film, paper and laminates Thickness range: -Rigid films: 10 – 200 micron -Soft films: 12 – 300 micron Machine Specification - SLIT UHS TURRET: -Web width:1300 / 1600 mm max -Unwind roll diameter: 1000 mm -Unwind roll weight: 1500 kg -Unwind roll cores: 3” and 6” I.D. -Finished roll diameter: 610 mm max -Finished roll cores: 3” and 6” I.D. -Slit width: 50 mm and up -Machine speed max: 600 m/min (depending on material type/quality) -Winding tension: 0.5 pli to 2.5 pli (11 - 45 kg) standard
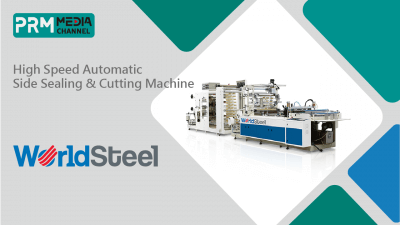
Plastic Bag Making Machine | WorldSteel
Suitable for a range of shapes folds and pockets, interlinking with other equipment to be able to make even more types of bags for easy exchange. Pattern types include: punching equipment for round holes, butterfly holes, utilizes handheld punching equipment for accuracy and can produce perforations for letter and packaging tear off strips. Using a vertical up and down heat sealing system and supersonic sealing line device. Provide extra parts for improved production accuracy and quality, including EPC edge sensor, servo motor to drive the machinery and an automatic conveyor to get your finished products to the packing section as soon as possible. Suitable for already perforated and/or folded films. 【Company Introduction】 World Steel Machinery Company is dedicated to making technological innovations and manufacturing packaging machines.They have the best engineering crew in the industry to provide total solutions which include design, customization and development. If you are looking for machines that produce, flower sleeves, diaper bags, book sleeves, self adhesive bags, handle bags, sandwich bags or more, then World Steel is the best choice for you.
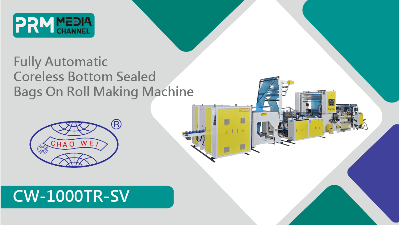
Fully Automatic Coreless Bottom Sealed Bags On Roll Making Machine | CHAO WEI
【Machine Spec & Features】 Bottom Sealed Bags On Roll Making Machine (Coreless) Film width: 600 mm / Thickness: 15 micron E.P.C Control & Rollers Device (E+L, German made) Length: 750 mm x Speed: 135 Pcs/Min Production Line Speed: 100M/Min Servo Driven Shuttle Type Sealing & Perforating Unit Two Sets Triangle Folders For Making Finished Roll With Small Width Machine Maintains High Speed Production By 4 Sets Rewinding Shafts While Producing Small Quantity Of Bags Per Roll 【Company Introduction】 Chao Wei Plastic Machinery is an advanced manufacturer of plastic bag making machine with more than 35 years of experience with ISO 9001 & CE certificates in Taiwan. One of the reasons for the excellence of Chao Wei’s machines is our dedication to research and development.